Table of contents:
Benefits of Using Professional Battery Testing Equipment Suppliers
How Reliable Battery Testers Reduce Production Defects
Understanding Charge and Discharge Cycles with Advanced Battery Tester Devices
Benefits of Using Professional Battery Testing Equipment Suppliers
Partnering with reliable battery testing equipment suppliers ensures you gain access to state-of-the-art lithium battery tester technology tailored to meet stringent industry requirements. These suppliers provide equipment with advanced features such as precision voltage measurements, automated charge-discharge settings, and modular designs for easy maintenance. The benefits extend beyond simple testing, including enhanced accuracy for detecting potential defects, scalability to cater to different production needs, and access to expert support from experienced battery test equipment manufacturers.Unlike conventional setups, leveraging a professional-grade battery tester streamlines your production process, minimizing downtime and ensuring quicker fault diagnosis. Battery testing equipment suppliers like those featured on DK Tester offer panel and software operation modes, enabling users to manage multiple testers from a single computer through TCP/IP protocols. This integration results in efficient workflows, reduced costs, and improved overall productivity. For manufacturers producing lithium-ion batteries, the added ability to analyze aging and anticipated wear ensures your end product satisfies both performance and safety benchmarks.
How Reliable Battery Testers Reduce Production Defects
Quality control becomes incredibly efficient when advanced battery testers are used. By deploying reliable battery testing equipment, manufacturers can pinpoint and prevent defects before batteries hit the market. Tools like DK Tester’s charge-discharge testers can perform high-precision testing by simulating real-world operational conditions. The equipment comes with features like polarity protection, voltage and current tolerance accuracy as low as 0.03%, and independent modules that prevent cascading failures.Production defects usually arise from inconsistencies in the energy storage capacity, variations in voltage tolerance, or issues in the discharge cycles. With the extensive capabilities provided by lithium battery testing solutions, these inconsistencies can be flagged early. Additionally, detecting errors in production lines means businesses can take corrective actions in advance, saving on recalls or potential liabilities. The simple operation interface and robust test-report export options make it easier for teams to analyze data while maintaining optimal production output. Ultimately, reliable testers not only protect your brand reputation but also afford long-term cost savings by reducing warranty claims and customer complaints.
Understanding Charge and Discharge Cycles with Advanced Battery Tester Devices
Charge-discharge cycles are the backbone of lithium-ion battery performance analysis. High-quality battery test equipment allows manufacturers to understand energy efficiency and longevity across cycles. Advanced testers such as the DSF20 lithium battery tester feature data sampling and charge-discharge curve analysis. These tools calculate metrics like voltage, capacity, and elapsed time with exceptional precision.Why does testing charge-discharge cycles matter? Each battery undergoes multiple usage phases, and inadequate testing can lead to critical failures when deployed in user devices. By using advanced lithium-ion battery testing equipment, businesses gain the ability to determine degradation patterns over numerous cycles. Furthermore, features like maximum cycle indices of up to 99 ensure that batteries adhere to aging benchmarks and perform efficiently over their lifetime. For electric vehicle manufacturers or consumer electronics producers, this capability is non-negotiable for delivering reliability in end products.
As battery production becomes more advanced and technical, manufacturers face mounting pressure to meet growing demands without compromising on quality. Tools such as advanced testers play a crucial role in this process, enabling manufacturers to streamline production, identify potential defects, and ensure that each battery meets the highest standards of reliability and performance. By integrating these tools into their workflows, manufacturers can keep pace with the rapid evolution of battery technology while delivering dependable products to consumers.
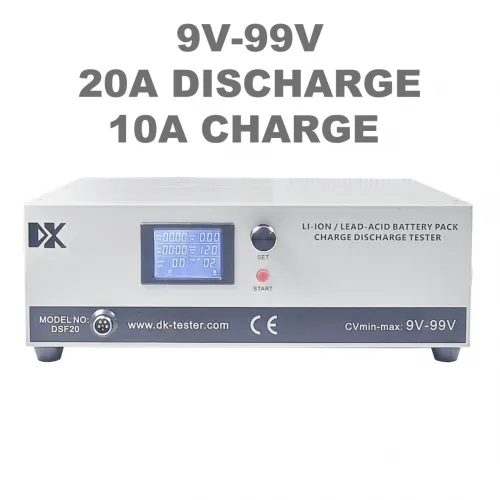
Comments
Post a Comment