Table of contents:
Ensuring Surface Finish Excellence in CNC Lathe Components
Precision Engineering and Material Innovation
Custom CNC Lathe Machining Parts for Industrial Equipment Markets
Ensuring Surface Finish Excellence in CNC Lathe Components
Surface finish quality has become a critical differentiator in the CNC machining industry, directly impacting component performance, durability, and aesthetic appeal. Modern CNC lathe machining parts require surface finishes that meet increasingly stringent specifications across various industries, from aerospace to medical devices. Zhichuanglian has recognized this trend and invested in advanced surface treatment technologies that deliver consistent, high-quality finishes across all their CNC products. The company's approach to wholesale CNC lathe machining parts emphasizes not just dimensional accuracy but also superior surface characteristics that extend component lifespan and improve operational efficiency. Advanced tooling technologies, including diamond-tipped cutting tools and ceramic inserts, are revolutionizing how manufacturers achieve exceptional surface finishes while maintaining cost-effectiveness. These innovations allow for faster cutting speeds without compromising finish quality, enabling manufacturers to meet tight production schedules while delivering premium results. Additionally, integrated measurement systems now provide real-time feedback on surface roughness, allowing operators to make immediate adjustments during the machining process. This technological integration ensures that every component meets exact specifications before leaving the production line, reducing waste and improving overall quality control processes.
Precision Engineering and Material Innovation
The future of CNC machining services lies in the convergence of precision engineering and advanced material science. As industries push the boundaries of what's possible with traditional materials, manufacturers are increasingly working with exotic alloys, composites, and engineered plastics that demand specialized machining approaches. Zhichuanglian's CNC lathe machining parts manufacturer capabilities have evolved to handle these challenging materials while maintaining the precision tolerances that modern applications require. Multi-axis machining centers are becoming standard equipment, allowing for complex geometries to be produced in single setups, reducing handling time and improving dimensional accuracy. This technological advancement enables manufacturers to achieve consistent results even when working with unfamiliar materials or complex part geometries. Predictive maintenance systems are also transforming how CNC equipment is maintained, using sensor data to anticipate potential issues before they affect production quality. These systems analyze vibration patterns, temperature fluctuations, and tool wear characteristics to schedule maintenance activities optimally, ensuring maximum uptime and consistent part quality throughout production runs.
Custom CNC Lathe Machining Parts for Industrial Equipment Markets
Industrial equipment markets are driving demand for increasingly customized CNC solutions that address specific operational challenges and performance requirements. Zhichuanglian's approach to custom manufacturing emphasizes collaboration with clients to develop tailored solutions that optimize both component performance and production efficiency. Advanced CAD/CAM software now enables rapid prototyping and design iteration, allowing manufacturers to test and refine designs before committing to full production runs. This capability is especially valuable in industrial equipment, where component failure can lead to costly downtime. Additive manufacturing is now integrated with traditional CNC processes, creating hybrid methods that combine the strengths of both. This allows for the production of complex internal geometries impossible with conventional machining, unlocking new possibilities for design and functionality. Quality assurance systems now include traceability features that track the entire manufacturing process, from raw material certification to final inspection. These systems ensure full documentation for critical applications and support continuous improvement through detailed production data analysis.
The trajectory of CNC machining services points toward an increasingly interconnected and intelligent manufacturing ecosystem. As technology continues to advance, companies that embrace innovation while maintaining focus on fundamental quality principles will lead the industry forward. The integration of artificial intelligence, advanced materials, and precision engineering capabilities creates unprecedented opportunities for manufacturers to deliver solutions that exceed traditional performance boundaries. Success in this evolving landscape requires continuous investment in both technology and expertise, ensuring that manufacturing capabilities keep pace with ever-changing market demands and customer expectations.
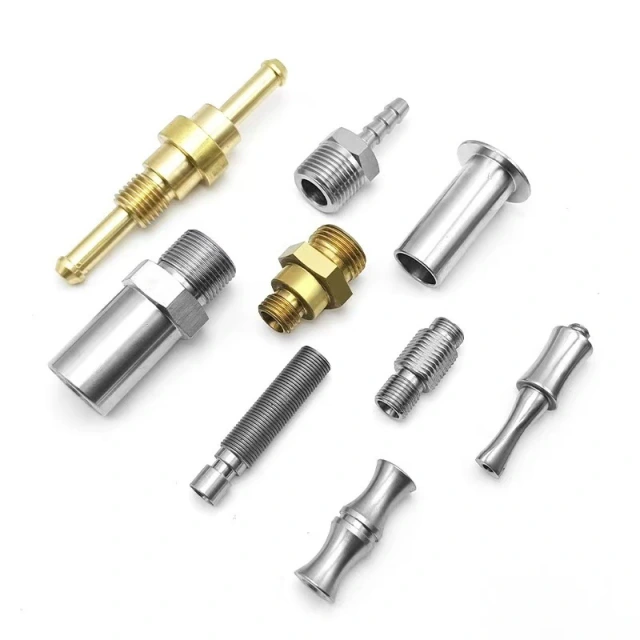
Comments
Post a Comment